摘 要:文章着重介绍了汽车动力总成自动化装配线上新研发采用的十字滑台浮动环节的机械结构、工作原理以及工作过程,通过此结构在实际现场使用的情况,对比分析了新型结构与传统结构的利弊区别,着重阐述了十字滑台浮动机构在汽车动力总成自动化装配线上所起的作用及其推广优势,以及由此带来的经济效益和社会效益。 关键词:十字浮动滑台机构;浮动调节;自动化装配;机器人;滑动导轨 引言[size=1em]在汽车动力总成自动化装配线上,以往在利用机器人或者桁架机械手抓取工件的时候都是刚性联接,虽然大部分也能装配上,但由于各个部件件装配的累积误差,还有工件随行板的一致性精度差的问题,即便在设备上设置了引导定位销,定位销引导部分做的很长很尖,勉强引入并装配到位,但同时也对定位销产生了很大的内应力,这种应力会传递给工件,对工件的质量也造成一定的损伤,另外,装配过程中也会对六轴机器人的精度损伤很大,影响了各个装配部件的寿命。针对上述问题,新近研发设计了一种新型的十字滑台浮动机构,克服了以往刚性联接中所存在的问题,解决了装配累积误差过大、随行工装板一致性精度差等因素而难于装配的问题,现在此十字浮动滑台机构已成功应用在汽车动力总成自动化装配流水线中,为主机厂提供了高品质高质量的发动机整机产品! 1 工作原理[size=1em]十字滑台浮动机构是加在机器人或者桁架机械手前的装置,可实现X 方向和Y 方向的浮动调节。实际应用中可以在机器人或者桁架机械手前端设置换枪盘实现生产中多品种产品自由兼容混线生产。如图1 所示,在十字滑台浮动机构的中间部分采用了X 向和Y 向双层空间十字交叉浮动导轨滑道,两侧采用锥形锁紧结构,锥形角度一般设置在5~15°,锥形面的粗糙度需要达到Ra0.8,锥形零件表面需要做氮化热处理,耐磨。机构下方联接机器人侧快换盘,工具侧快换盘装在工件夹具上,不同工件有各自工件夹具,当装配开始前,机器人会带着十字滑台浮动机构以及不同的工件夹具按照待装配工件的定位位置进行装配轨迹的人工调试,设计自动装配程序,此时,锥形锁紧结构处于锁紧状态;自动装配开始,机器人抓取工件时,快要到接触到工件的时候,锁紧气缸杆伸出,锥杆下移,锥形公母件脱离打开,此时X、Y向的导轨呈自由浮动状态,机器人继续下探抓取工件,当抓取完成后,机器人带动工件抬起,脱离原定位位置后锁紧气缸缩回,十字滑台浮动机构锁紧,机器人带着工件按照设定程序轨迹到达需要装配的另一工件上方,十字滑台浮动机构再次打开,机器人下探自动认销,浮动滑台随销滑动,浮动量超误差量,可以轻松实现快速自动无应力装配;工件装配完成后,夹具松开,机器人上移,脱离定位导向销,锁紧气缸缩回,十字浮动机构再次锁紧,机器人带着夹具回至原位,一组工件的自动装配工作完成。 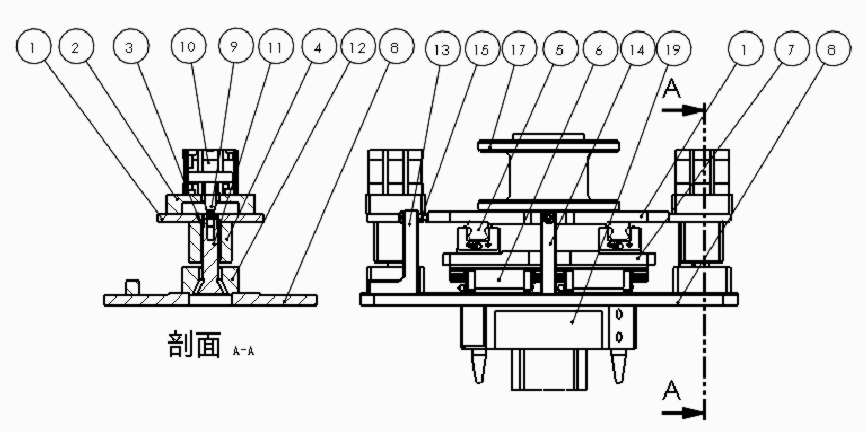 [size=0.8em]图1 十字浮动机构装配示意图 [size=0.8em]1、上板 2、气缸连接板 3、滑套 4、固定套 5、Y 向导轨 6、X 向导轨7、中板 8、下板 9、气缸接头 10、气缸 11、锥形杆 12、锥套13、X 向挡块 14、Y 向挡块 15、缓冲器 17、连接法兰18、工具侧快换盘 19、机器人侧快换盘
2 结构及工作过程[size=1em]以汽车发动机缸体缸盖自动化合箱装配为例进行详细介绍。 2.1 结构[size=1em]图1 为十字滑台浮动机构装配示意图,如图所示,装在上板1 上的连接法兰17 直接与机器人相连,上板两侧装有气缸连接板2,连接板上安装气缸10,气缸接头9 上与气缸相连,下与锥杆11 相接,锥杆锥头部分落于锥套12 内,锥杆直头部分含在滑套3 和固定套4 内,锥杆与锥套的半径间隙决定机构的浮动量,一般半径间隙设计为5~10mm,气缸行程视浮动量而定,此为锥形锁紧部分,X 向左右两侧各一套;上板下方安装Y 向导轨5,中板7 上方安装Y 向滑块,下方安装X 向导轨6,下板8 上方安装X 向滑块,下方安装机器人侧快换盘19,与安装在夹具上的工具侧快换盘18 对接,X向、Y 向导轨滑块各自配套,滑块行程为浮动量的7~10 倍,此为中间十字滑台部分;另外,下板上方还安装了用于限位的X 向挡块和Y 向挡块,通过缓冲器实现X、Y 双向限位;图2 为十字滑台浮动机构三维模型图。 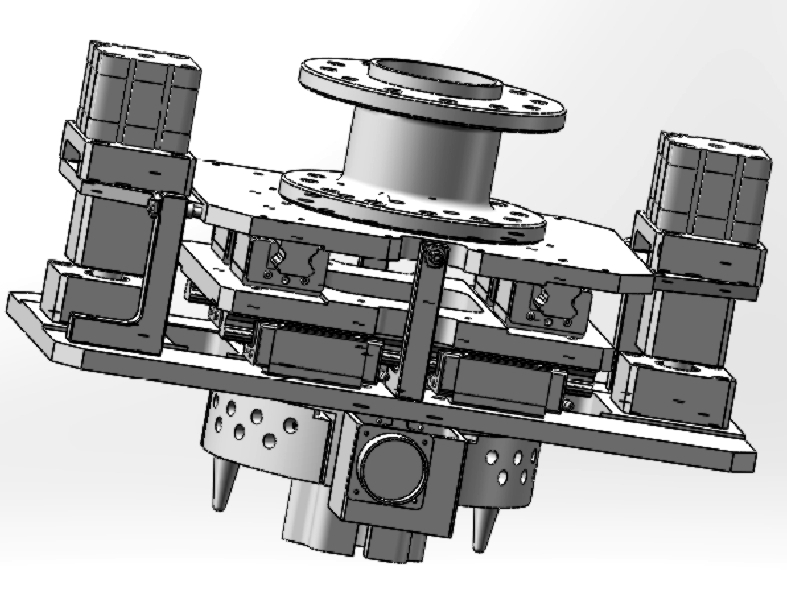 [size=0.8em]图2 十字浮动机构三维模型
2.2 工作过程[size=1em]2.2.1 工作内容及要求介绍 [size=1em]本套机构用在六轴机器人将缸盖总成从缸盖分装线转移到缸体线上,并将缸盖总成装到缸体上、自动找正定位圆销自动找正合箱,从而实现全自动无应力快速合箱装配。 [size=1em]2.2.2 工作过程介绍 [size=1em]自动装配开始前,机器人带着十字滑台浮动机构以及不同机型的缸盖夹具按照待装配缸体线和缸盖线的固定定位位置进行装配轨迹的人工调试,设计自动装配程序,此时,锥形锁紧结构处于锁紧状态;调试结束后,首先缸盖托盘带着缸盖进入缸盖线固定工位,预挡料器落下,工位挡料器抬起,托盘输送到位,工件检测装置检测有无工件,检测托盘姿态,读写头读码块信息,二次定位装置上的插销在气缸的作用下插入托盘底部销孔,定位缸盖托盘;同时缸体托盘带着缸体进入缸体线固定工位,预挡料器落下,工位挡料器抬起,托盘输送到位,工件检测装置检测有无工件,检测托盘姿态,读写头读码块信息,二次定位装置上的插销在气缸的作用下插入托盘底部销孔,定位缸体托盘;当缸体、缸盖均完成定位后,自动装配工作开始,首先,机器人带着十字滑台浮动机构读取机型,根据机型判别与其匹配的缸盖夹具,机器人侧快换盘与识别到的缸盖夹具上的工具侧快换盘自动对接,缸盖夹具就装到机器人上了;随后,机器人带着缸盖夹具抓取缸盖,在缸盖上方50~100mm 处,锁紧气缸杆伸出,锥杆下移,锥形结构打开,轴向间隙可达3~7mm(即浮动量,浮动量根据不同的使用工况下非标设计。),此时X、Y 向的导轨呈自由浮动状态;同时,缸盖夹具上的夹爪通过气缸打开,机器人继续下移,通过夹具上的一面两销,与缸盖定位,缸盖夹具上的夹爪通过气缸闭合,将缸盖夹紧;当抓取完成后,机器人带动缸盖抬起,脱离原定位位置50~100mm 处,锁紧气缸缩回,十字滑台浮动机构锁紧;机器人带着缸盖按照设定程序轨迹到达缸体上方50~100mm 处,锥形锁紧气缸工作,十字滑台浮动机构再次打开,机器人下移自动认销(该定位销设计在缸体上的居多,缸盖的相应位置为销孔),定位销采用一圆一菱两点定位的模式,定位销头部设计成锥形导向,在定位销的锥形导向引导下,十字滑台浮动机构X、Y 向滑块随之浮动调节,缸盖沿着定位销顺利的落在缸体上,实现了快速自动无应力装配。定位后,缸盖夹具夹爪气缸松开,机器人移至上方50~100mm 处,脱离缸盖,锥形锁紧气缸缩回,十字浮动机构再次锁紧,机器人带着缸盖夹具回至原位,完成该机型的一次缸盖和缸体的自动装配过程。之后,缸体线挡料器打开,插销气缸缩回,缸体托盘脱离定位,缸体随轨道至下一工位;至此,该装配循环结束,转入下一组缸体缸盖的自动装配。 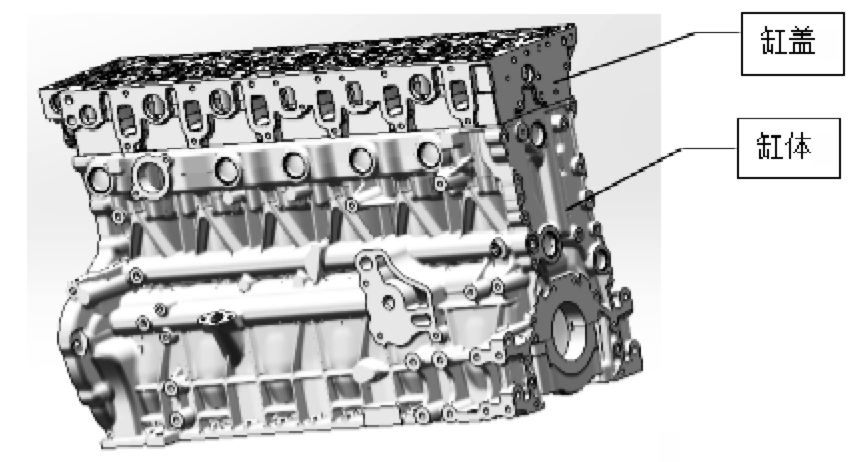 [size=0.8em]图3 缸盖缸体合箱三维模型
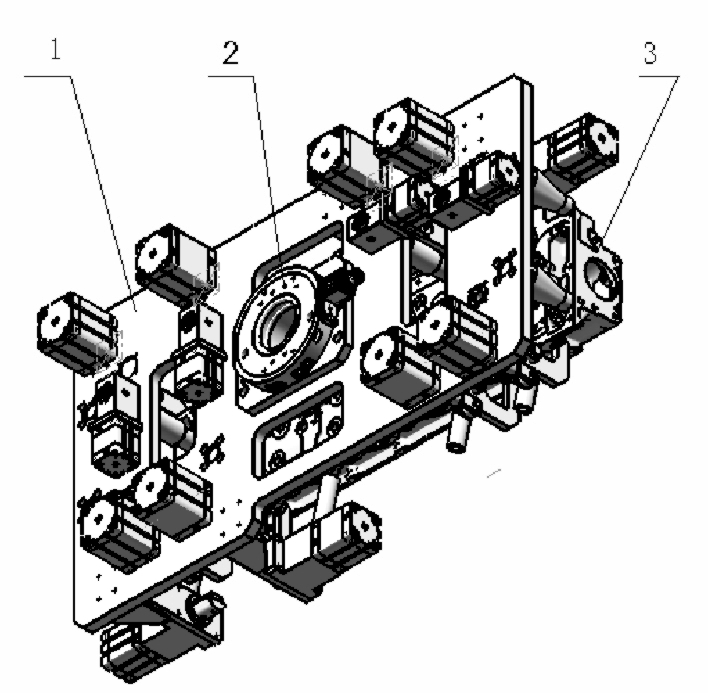 [size=0.8em]图4 缸盖夹具三维模型 [size=0.8em]1.缸盖夹具 2.机器人工具侧快换盘 3.缸盖
3 装配过程中定位偏差的产生[size=1em](1) 在缸盖与缸体自动装配过程中,有6 次定位销配合,即: [size=1em]1)缸盖二次定位与缸盖托盘间的插销配合; [size=1em]2)缸盖托盘与缸盖间的定位销配合; [size=1em]3)缸盖与缸盖夹具间的定位销配合; [size=1em]4)缸体二次定位与缸体托盘间的定位销配合; [size=1em]5)缸体托盘与缸体间的定位销配合; [size=1em]6)缸盖/与缸体间的定位销配合。 [size=1em]各配合件间均用一圆销一菱销双销定位,配合精度为:孔为H7,销直径为孔名义最小尺寸-0.05mm 后g6,各机型缸体缸盖的累积加工误差按120%计算,得出六轴机器人从抓取缸盖到将缸盖装配至缸体上全过程的累积定位误差,从下表1 中可以看出,最大误差可达0.6mm,如果采用刚性联接,势必造成缸体与缸盖间的定位销在定位导向的引导下强行装入,在缸体与缸盖间以及机器人机器手臂内产生很大的内应力,对工件质量不利,对机器人寿命及精度不利,而十字滑台浮动机构浮动量5mm,为定位累积偏差的8.3~13.9 倍,可以很轻松的解决装配定位误差的问题、加工高精度难保证的问题、部件间长时间变形损耗的问题。此结构的应用,它有力的保护了工件质量,保护了机器人,保护了生产链中零部件供应的达成率。同时大大的提高了各个行业的生产装配效率。 [size=0.8em]表1 装配过程中的累积定位偏差单位:mm 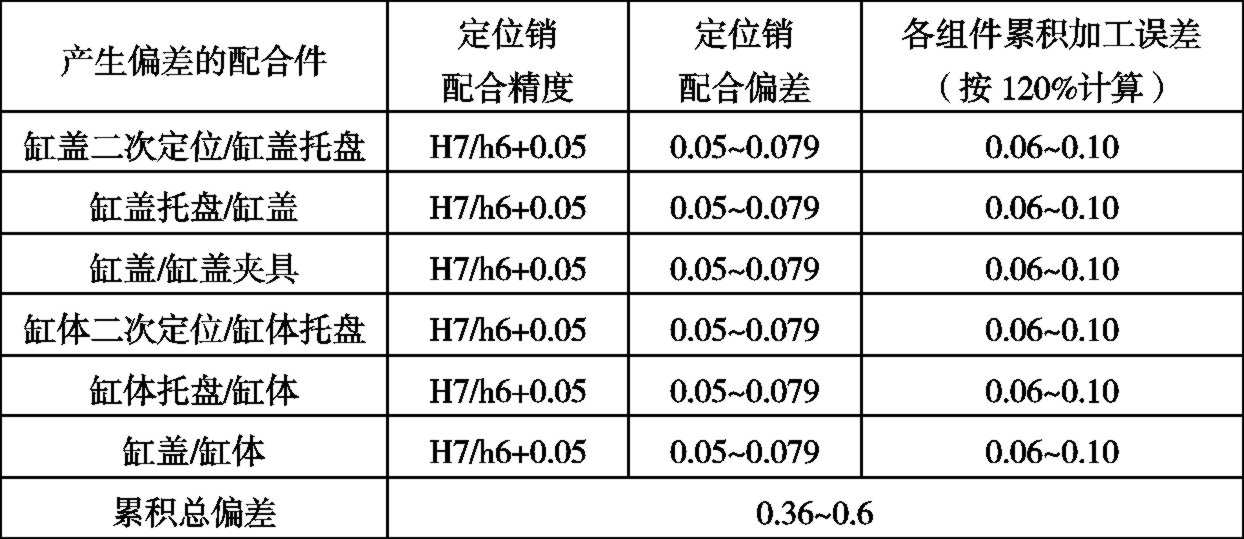 [size=0.8em]注:以定位销均为φ16 为例计算
[size=1em](2)在自动化装配线中,工件的批量随行板(即托盘)的一致性精度很难保证,对于汽油机1.0~2.4L 发动机托盘的一致性精度通常在0.1~0.2mm 左右。对于柴油机6~20L 发动机托盘的一致性精度通常在0.5~1mm 左右。但是在实际现场情况中,托盘的一致性精度往往都比理论数值相差很多,从而就造成了自动化抓取定位、合箱装配等小间隙装配设备造成了非常大的难度。尤其是在近几年中,柴油机的市场需求愈来愈多,随之对应的柴油机的装配产能提高了很多,很多厂家进行装配线的自动化程度升级改造,特别在缸体、缸盖自动化上线、缸体缸盖自动化合箱设备方面,需求格外之多,同时也对装配质量提出了很高的要求。那么通过本文上述的十字滑台浮动机构,可以很好的解决托盘一致性精度差的疑难问题,从而降低了对批量托盘的一致性精度要求,从而实现降本增效! 4 适用范围[size=1em]本文介绍的十字滑台浮动机构适用于动力总成自动化装配线上定位环节多,累积定位偏差大的场合,如汽车动力总成的自动化装配线上都可以应用。比如缸体自动化上线、缸盖自动化上线、缸体和缸盖之间自动化合箱、DCT 变速箱前后壳自动化合箱、轻量化卡车变速箱前壳体、后壳体自动化合箱等工位。 5 结论[size=1em]本机构结构简单、操作方便、安全可靠,适用性强,弥补了刚性联接认销困难、安装成功率低、内应力大等不足,既提高了装配效率又起到了保护产品工件质量的作用,避免在自动化过程中划伤工件,保护机器人内部环节不受损伤,确保了产品装配质量,大大提高了六轴机器人、机械手臂的使用寿命,保证了机器人的装配精度,同时也缓解了对工件加工精度的要求,对设备的部件装配精度也降低了要求,此结构应用可以在动力总成自动化装配线上得到大量的应用,同时可以把此应用推广到其他的自动化装配领域中,比如新能源电池PACK 线,3C 摄像头模组自动化装配等领域。其大批量推广应用后,必将产生显著的经济效益及积极的社会效益。 [size=1em]参考文献 [size=1em][1] 成大先,王德夫等.机械设计手册[M].化学工业出版社,2004. [size=1em][2] 金振华等.组合机床及其调整和使用[M].机械工业出版社,1990. [size=1em][3] 王凡等.实用机械制造工艺设计手册[M].北京机械工业出版社,2008. [size=1em][4] 刘巽尔编著.形状和位置公差[M].北京中国标准出版社,1990. [size=1em][5] 林约利等.简明金属热处理手册[M].上海科学技术出版社,1987. [size=1em][6] 金振华等.组合机床及其调整和使用[M].机械工业出版社,1990. [size=1em][7] 戴曙等.金属切削机床设计[M].机械工业出版社,1990.
[size=1.8em]A Brief Analysis on the Application of Floating Mechanism of Cross Slide Table in Automatic Assembly Line of Automobile Powertrain [size=1em]He Yulai
( Dalian Zhiyun Automated Co.Ltd., Liaoning Dalian 116011 ) [size=1em]Abstract: Automotive powertrain automated assembly line in the cross slide floating mechanism application is analysed in this paper introduces the research and development of new vehicle powertrain automatic assembly line using the cross slide floating section of mechanical structure, working principle and working process, through this structure at the scene of the actual use situation, comparative analysis the advantages and disadvantages of the new structure and traditional structure difference, emphatically expounds the cross slide floating mechanism in the role of the automotive powertrain automatic assembly line and its advantage, and the resulting economic and social benefits. [size=1em]Keywords: The cross slide guide floating structure; Flostng adjustment; Automatable assembly; Robot; Slide guide
|